I. Introduction
- Background: The acceptance phase is a critical step in the purchasing process of used excavators, directly influencing the performance and lifespan of the equipment. During this phase, a thorough inspection can identify potential issues, helping to avoid high repair costs and safety hazards in the future.
- Purpose and Significance: This guide aims to provide buyers with a systematic inspection process, assisting them in effectively identifying and assessing the condition of used excavators, ensuring reliability and protecting their investment.
II. Preliminary Inspection
1. Visual Inspection
- Overall Condition: Start with a comprehensive visual inspection of the equipment, looking for visible damage, rust, cracks, and other defects, especially in critical areas such as the chassis and hydraulic components.
- Identification and Labels: Confirm that the equipment’s model, production date, serial number, and all relevant labels are clear and visible, ensuring consistency with sales documents.
2. Equipment History Records
- Maintenance Records: Review the maintenance and service history of the equipment to understand its usage background, including:
- Regular Maintenance: Check whether regular maintenance has been performed on schedule and review the status of replaced parts.
- Failure Records: Look into past failure records to assess the frequency and types of repairs.
- Operating Hours: Verify the operating hours of the equipment through the dashboard or work logs to evaluate its usage level and determine wear and tear.
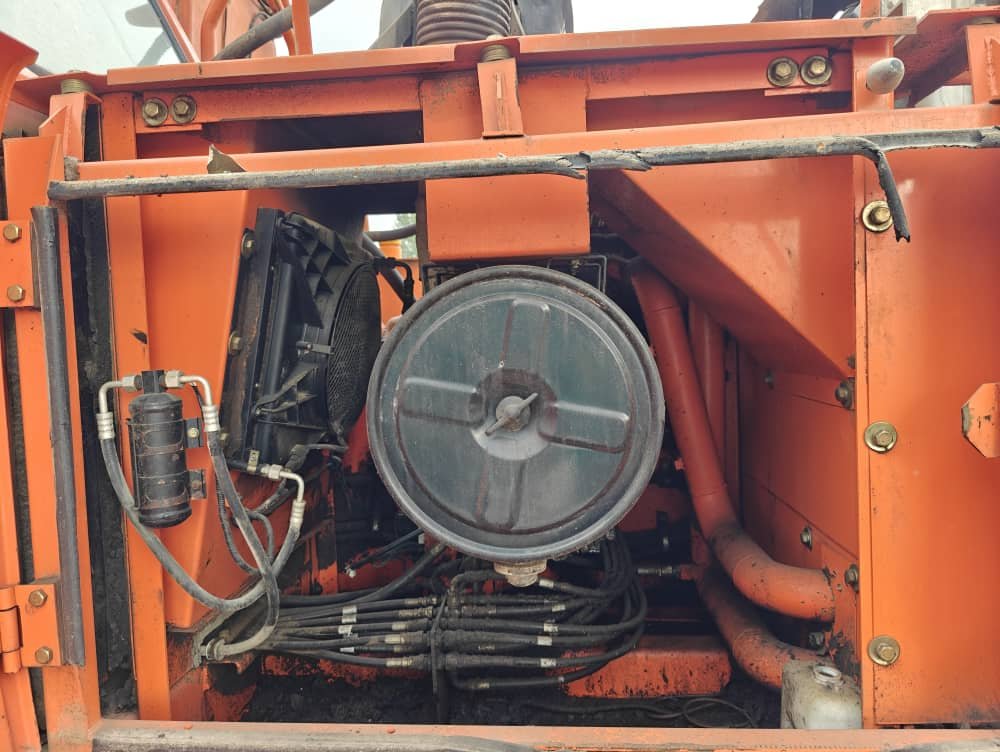
III. Key Component Inspection
1. Engine
- Starting Performance: Test the engine’s starting performance, listening for unusual noises or vibrations that may indicate issues.
- Fluid Checks: Inspect the status and levels of engine oil, coolant, and hydraulic oil:
- Engine Oil: Assess the oil’s color and viscosity, confirming whether it needs replacement.
- Coolant: Check the coolant level and quality to ensure the engine does not overheat during operation.
- Hydraulic Oil: Evaluate the cleanliness of the hydraulic oil, ensuring there is no contamination or foul odor.
2. Hydraulic System
- Hydraulic Lines: Inspect the integrity of hydraulic lines, checking for leaks, cracks, or signs of wear, and ensuring connections are secure.
- Hydraulic Oil: Assess the quality of the hydraulic oil, confirming it is free from contamination to prevent hydraulic system failures.
3. Track System
- Tracks and Sprockets: Examine the wear condition of the tracks and the sprocket tooth shape, ensuring there are no signs of significant wear or missing parts.
- Roller Inspection: Check the state of the drive wheel, idler wheel, support rollers, and carrier rollers individually:
- Drive Wheel: Inspect the tooth shape and contact surface for wear.
- Idler Wheel: Ensure it rotates smoothly without binding.
- Support and Carrier Rollers: Look for deformation or excessive wear.
IV. Operational Function Testing
1. Mobility Function
- Walking Stability: Test the stability of the equipment while moving, observing for any shaking or unusual noises to ensure stable operation.
- Steering Responsiveness: Check the steering system’s responsiveness, ensuring it operates smoothly and effectively on various terrains.
2. Additional Functions
- Digging Function: Test the bucket’s lifting, rotating, and tilting functionalities to confirm smooth operation without unusual sounds.
- Auxiliary Equipment: Inspect the operational status of all auxiliary devices (such as bucket teeth, grapples, etc.) to ensure they function properly.
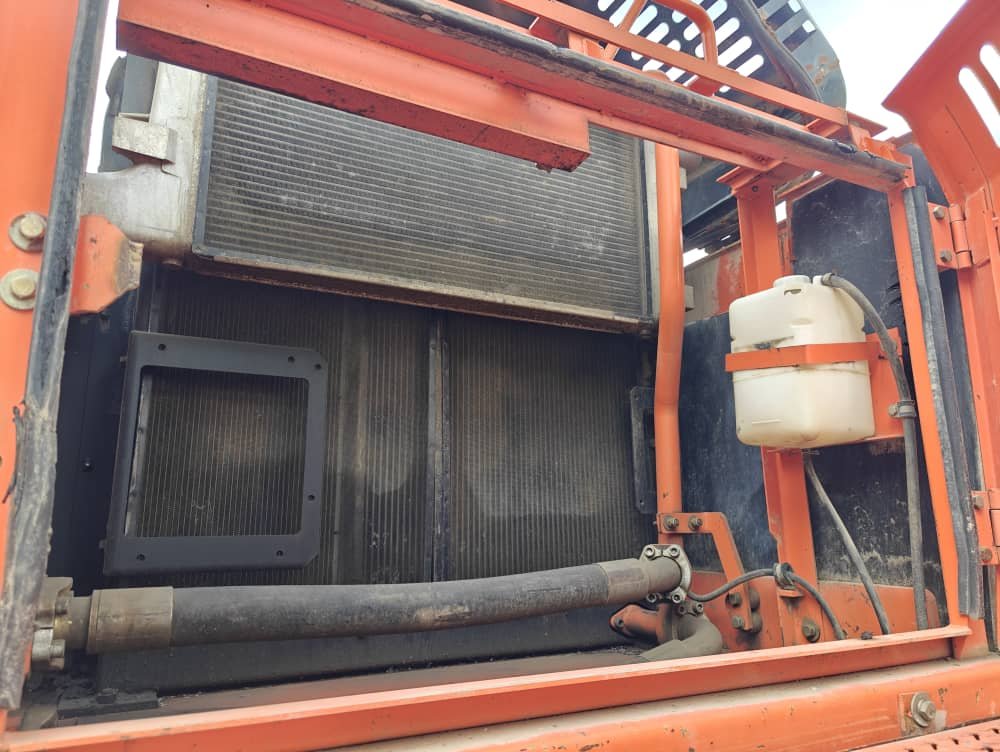
V. Safety Equipment Inspection
- Braking System: Examine the performance of the braking system, testing its sensitivity and effectiveness to ensure the equipment can stop quickly when needed.
- Safety Warning Labels: Confirm that all safety labels and warning signs on the equipment are intact and meet safety usage standards.
VI. Summary and Recommendations
- Assessment of Inspection Results: Summarize the findings of the inspection, evaluating the overall condition of the equipment and identifying potential issues that need attention.
- Follow-up Action Recommendations: Based on the inspection results, provide maintenance and care recommendations to help users better operate the equipment, such as:
- Necessary Repairs: If significant issues are found, recommend timely repairs or part replacements.
- Regular Maintenance Plan: Suggest establishing a regular maintenance schedule to ensure the equipment remains in good condition during use, extending its lifespan.