I. Introduction
- Background: In engineering and construction projects, excavators are essential equipment. They play a critical role in earthworks, foundation construction, mining, and other fields. Clearly defining requirements and budgets is crucial to ensure the smooth progress of projects, as improper equipment selection can lead to delays and cost overruns.
- Purpose and Significance: By clearly outlining the models, specifications, and quantities of excavators needed, project managers can make informed purchasing decisions, optimize resource allocation, and effectively enhance work efficiency while reducing operational costs.
- Market Research: Analyze the types and prices of excavators currently available in the market to understand industry trends and technological advancements. This process will help identify the most suitable equipment for project needs and evaluate the competitiveness of different brands and suppliers.
- Stakeholder Communication: Engage with the project team, finance department, and suppliers to ensure transparency in requirements and budget. Cross-departmental collaboration can provide a more comprehensive range of opinions and suggestions, avoiding decision-making errors due to information asymmetry.
- Long-term Planning: Consider the future use and maintenance plans for the excavators to ensure purchasing decisions align with long-term goals. Evaluating the equipment’s lifespan, maintenance costs, and potential upgrade needs can help formulate a more forward-looking investment strategy.
II. Defining Excavator Requirements
1. Project Requirements Analysis
- Project Type: Determine the nature of the project (e.g., construction, mining, earthworks), as different projects have varying excavator requirements. For instance, mining projects may require higher performance and durability, while urban construction projects might focus more on compact and flexible equipment.
- Work Environment: Analyze the terrain and environment for excavation work (e.g., urban, rural, mountainous), which will influence the selection and configuration of excavators. For example, in narrow urban settings, small excavators may be more advantageous, while large excavators may be more efficient in open mining areas.
2. Excavator Models and Specifications
- Model Selection: Choose the appropriate excavator model (small, medium, large) based on project requirements, while also considering the reputation and after-sales service of the brand. Selecting a suitable model based on different operational needs can significantly enhance work efficiency.
- Key Specifications:
- Operating Weight: Different operating weights are suited to different work requirements. Heavier excavators generally offer greater stability and digging capacity, making them suitable for heavy-duty tasks.
- Digging Depth and Reach: Determine the required digging depth and operational range based on project needs. For example, foundation work may require deeper digging capabilities, while road construction may emphasize a broader operational range.
- Engine Power: Consider the power requirements of the excavator to ensure efficient operation. Engine power directly affects the performance and efficiency of the excavator, making it crucial to choose the right power level.
- Additional Features: Such as rotating buckets and hydraulic systems, select appropriate additional features according to project needs to enhance operational flexibility and efficiency.
3. Quantity Requirements
- Work Cycle: Determine the number of excavators needed based on the project timeline and workload. Urgent projects may require more equipment to complete tasks within a tight timeframe.
- Multi-tasking Needs: Assess whether the project requires multiple operations to be conducted simultaneously, which will influence the number of excavators needed. For instance, in large construction projects, multiple teams may need to conduct earthworks and foundation work simultaneously, resulting in increased equipment demand.
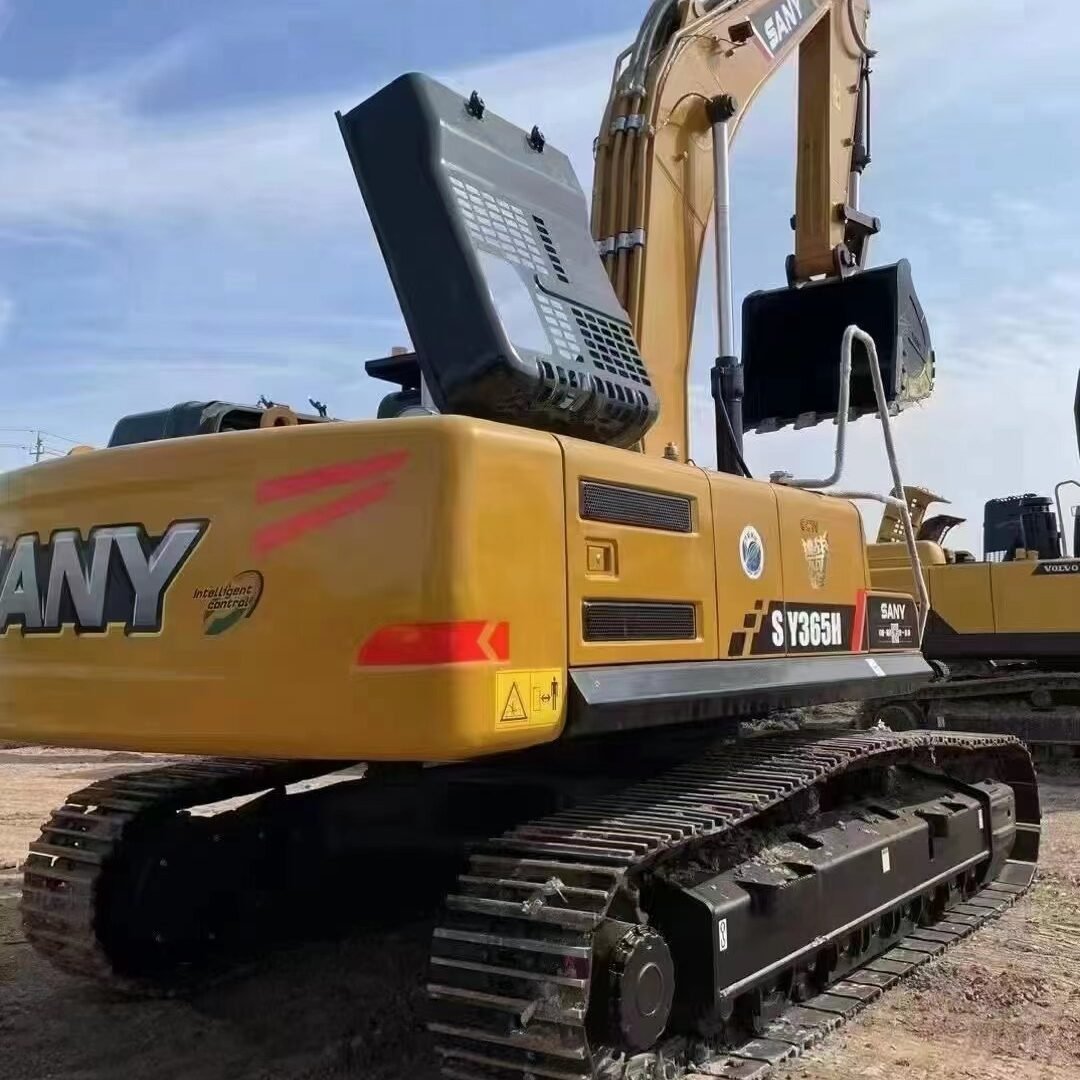
III. Budget Range Determination
1. Cost Composition Analysis
- Purchase Cost: Includes the purchase price of the excavators and associated taxes. When procuring, consider quotes from different suppliers and compare them to obtain the best price.
- Operating Costs: Include fuel, maintenance, insurance, and other daily operating expenses. Understanding the fuel efficiency and maintenance requirements of the excavator helps accurately estimate long-term operating costs.
- Depreciation and Residual Value: Consider the depreciation rate of the excavator and its future residual value to assess long-term investment returns. Proper depreciation calculations can help businesses accurately reflect changes in equipment value on financial statements.
2. Budget Range Setting
- Total Budget: Determine the overall budget range based on project scale and funding sources. Ensure the budget includes all necessary expenses to avoid delays or quality issues due to insufficient funding.
- Flexibility Considerations: Allow for budget flexibility to account for unexpected expenses, such as equipment damage or market price fluctuations that could affect the overall budget.
IV. Risk Assessment and Management
1. Risk Identification
- Equipment Failure Risk: Excavators may experience failures during use, affecting work progress. Identify potential failure types and their impact on the project, and develop corresponding contingency plans.
- Market Volatility Risk: Equipment prices, fuel costs, and other operating expenses may fluctuate due to market volatility, impacting budget accuracy.
- Legal and Regulatory Risks: Different regions may have varying legal and regulatory requirements for the use of construction equipment, necessitating compliance to avoid project delays due to legal issues.
2. Risk Response Strategies
- Equipment Maintenance Plan: Develop a regular maintenance and inspection schedule to minimize the likelihood of failures and ensure the excavator operates in good condition.
- Cost Control Measures: Negotiate with multiple suppliers to control equipment purchase and operating costs and establish a budget alert mechanism for timely adjustments.
- Compliance Training: Provide legal and regulatory training for relevant operators to ensure all operations comply with local laws, avoiding legal risks from non-compliance.
3. Continuous Monitoring and Evaluation
- Project Progress Monitoring: Regularly check project progress and equipment usage to ensure implementation according to plan and timely resource adjustments.
- Budget Execution Evaluation: Continuously monitor budget execution and assess actual expenditures against the budget to make necessary adjustments, ensuring the project remains within budget.
V. Summary and Recommendations
- Key Takeaways: Reiterate the importance of clearly defining excavator models, specifications, quantities, and budget ranges to ensure efficient procurement. Accurate requirement analysis and budget setting provide a foundation for the smooth execution of projects.
- Recommended Measures: Regularly evaluate needs and budgets, staying aligned with market dynamics for flexible adjustments. Ongoing market monitoring and equipment evaluations will help businesses maintain competitiveness in changing environments and ensure the appropriateness and effectiveness of equipment investments.
- Building Supplier Relationships: Establish long-term cooperative relationships with multiple equipment suppliers to quickly obtain equipment when needed and enjoy more competitive pricing and services.
- Training and Support: Provide necessary training for operators to ensure they can fully utilize the equipment’s capabilities and enhance work efficiency. Maintain communication with suppliers to obtain timely technical support and services.